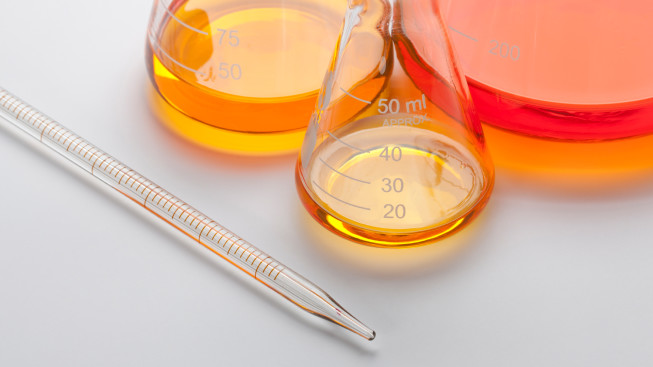
The world of lubrication is one of diversity: Each machine, application and set of operating conditions demands a particular combination of lubricant properties and functions. These demands create the need for a broad spectrum of lubricant formulations, and base oils alone are not enough to deliver the necessary performance levels machines demand in most situations. To perform its intended functions, a lubricant must be carefully and precisely blended with the appropriate additives. Each additive in a lubricant formulation either enhances the base oil’s innate properties or introduces additional properties.
Take a look at some common types of additives and what they do:
Antioxidants
Oxidation, the process of lubricant degradation due to contact with oxygen (from air or water), shortens a lubricant’s service life. Oxidation promotes varnish and sludge formation as well as rust and corrosion — all issues which may damage equipment and lead to increased maintenance costs and downtime. It also increases lubricant viscosity, adversely impacting lubricant performance.
Antioxidants help impede oxidation and its harmful effects, thereby prolonging a lubricant’s service life and providing better equipment protection.
Viscosity Modifiers
Viscosity, a fluid’s resistance to flow at a given temperature, is one of the most important properties of a lubricant. Maintaining the right viscosity is vital for ensuring that (a) the lubricant flows to where it is needed in a timely manner and (b) it provides the level of protection that the application requires.
A lubricant’s viscosity changes inversely with temperature: It increases under falling temperatures, limiting flow. And it decreases at higher temperatures, diminishing the fluid’s protective capabilities. Viscosity modifiers can help moderate the extent to which a lubricant’s viscosity changes in response to temperature fluctuations. This helps the lubricant maintain a more consistent flow rate and more reliable protection.
Pour-Point Depressants
A lubricant’s pour point, the lowest temperature at which it will flows, is a critical property for cold-temperature applications. Cold temperatures can cause wax crystals to form in some lubricants, hindering flow. If a lubricant fails to flow on time to where it is needed, problems ranging from increased friction and wear to equipment seizure/failure may result.
Pour-point depressants help restrict the formation and behavior of wax crystals to help maintain a lubricant’s flow in low temperatures.
Anti-Wear Agents
Anti-wear agents react with metal surfaces, forming a sacrificial film layer to help prevent metal-on-metal contact. By reducing friction and wear, anti-wear agents may help prolong component life. These additives generally are suitable for moderate-temperature, moderate-load applications, especially if excessive sliding or rolling may occur.
Extreme-Pressure Agents
Like anti-wear agents, extreme-pressure (EP) agents react with metal surfaces, forming a layer to reduce friction and help prevent welding, scoring and seizure. EP agents are designed for use in higher temperatures and with heavier loads than anti-wear agents.
Friction Modifiers
These additives attach to metal surfaces to cushion them from friction. The usefulness of friction modifiers is limited to conditions with light frictional contact, such as sliding and rolling. For heavier frictional contact, anti-wear agents or EP agents usually are more appropriate.
Metal Deactivators
The active ions in nonferrous metals (e.g., copper and aluminum alloys) tend to promote oxidation in lubricants, degrading the oil and shortening its service life. Metal deactivators form an inactive film on metal surfaces to reduce or prevent this negative interaction between metals and lubricants. These additives also help reduce corrosion.
Rust And Corrosion Inhibitors
Rust and corrosion damage metal parts, often resulting in costs for repairs or replacement. Rust and corrosion inhibitors can help protect against this damage in one of two ways: Some of these additives are absorbed on metal surfaces, forming a protective film to guard against oxygen, acids and other corrosive substances. Other additives in this category are designed to neutralize the harmful substances, rendering them innocuous.
Anti-Foam Agents
Foaming, the formation of a persistent layer of bubbles on a lubricant’s surface, can lead to insufficient lubrication — and consequently increased friction, wear and possible equipment failure. Foaming also encourages oxidation, diminishing fluid life.
Anti-foam agents reduce the oil’s surface tension, causing air and gas bubbles to collapse. This helps prevent the bubbles from collecting and forming a persistent foam layer.
Seal-Swell Agents
When seals in lubrication systems shrink, contamination or leaks may occur. Seal-swell agents are absorbed by the elastomeric material in a seal, causing the seal to expand. This closes gaps to help prevent leaks and contamination, and it extends the seal’s useful life.
Demulsifiers
Water is one of a lubricant’s greatest hazards. It can:
- Hasten the oxidation of a lubricant, shortening its service life.
- Encourage the buildup of sludge and varnish, and cause metal parts to rust and corrode.
- Deplete the lubricant’s film strength, making components more vulnerable to wear.
- Strip the lubricant of vital additives, impacting its performance and protective capabilities.
Many oils separate well enough from water on their own, but some base fluids and additives are prone to water contamination. Demulsifiers enhance the separation of water from lubricants for easier removal of water from the system.
Emulsifiers
Some applications call for lubricants that are emulsified water and oil mixtures. Emulsifiers may be used in these cases to reduce the surface tension of water, helping it mix thoroughly with oil.
Detergents
When lubricants degrade (due to contamination, heat, age or other causes), the byproducts of degradation can form sludge and varnish. These deposits may lead to a multitude of problems such as increased friction, wear and corrosion of component surfaces; sticking and failure of parts; clogging of filters, orifices and ports; increased heat; and inadequate lubrication.
Detergents neutralize and dissolve degradation byproducts to help prevent the formation of sludge and varnish.
Dispersants
Like detergents, dispersants combat the formation of sludge and varnish by targeting the byproducts of lubricant degradation. Dispersants bond to the byproducts and keep them dispersed and suspended in the lubricant, preventing them from gathering and forming sludge or varnish.
Expert Guidance, Ideal Solutions
Isel’s expertly blended formulations enhance lubricant performance, protection and fluid life without compromise. Don’t settle for less than what you and your customers deserve. Contact Isel today for the ideal formulations for your customers’ needs.
Relevant Entries in this Category that May Interest You:
Isel is Now Part of DuBois Chemicals!
In 2020, Isel joined the DuBois Chemicals team! DuBois/Isel is proud to continue the tradition of manufacturing refrigeration solutions specializing in...
Read MoreISEL to exhibit at Best Practices Compressed Air EXPO – 2021
Visit ISEL at the Best Practices Compressed Air EXPO which is held at the Renaissance Schaumburg Convention Center Hotel in...
Read MoreMAKE-A-WISH TURNS 40 AND ISEL SHOWS THEIR SUPPORT
April 2020 On April 29, 1980, the first wish was granted. A seven-year-old boy who yearned to be a police...
Read More