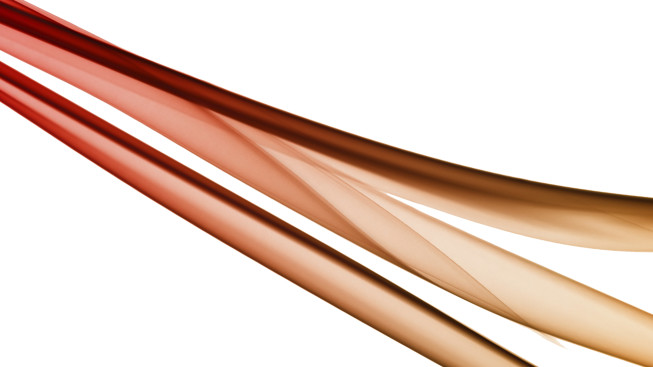
In many facilities, air compressors are responsible for a significant portion of the plant’s energy usage. And sometimes, a facility’s air compression system is the “heart” that keeps the plant’s operations in action. If an air compressor doesn’t work properly, a facility could experience substantially higher energy and maintenance costs. Proper lubrication of the air compressor may help avoid these problems. It helps the air compression system run more reliably and efficiently, thereby minimizing energy costs, repair costs and downtime.
What Is “Proper” Lubrication?
The answer depends on specifics such as the type of compressor, the application and the operating conditions.
Air compressors vary in type — rotary screw, rotary vane, reciprocating, centrifugal and more. With each type, the specific function of the lubricant may differ to some extent. For reciprocating compressors, the key functions of a lubricant are to minimize wear on cylinders and rings, and to reduce or eliminate carbon formation on the valves, thus helping to prevent overheating. For centrifugal units, the focal points may be on resisting gear and bearing wear in addition to preventing varnish formation. Lubricants for oil-flooded rotary screw compressors, should help absorb compressor heat for subsequent dissipation in the oil cooler, lubricate bearings and provide good sealing properties. These lubricants also should resist water contamination, which can result in loss of lubricity and additives in condensate.
All of the above factors will influence what formulation of base stocks and additives will provide optimum performance, protection and service life for the compressor.
Added bonus: Proper lubrication minimizes friction. Because friction causes more heat and demands more energy consumption to cool the unit sufficiently for safe operation, reducing friction means less power usage and lower energy costs.
Desired Characteristics
In general, an air compressor lubricant should possess the following properties:
The appropriate viscosity and a sufficiently high viscosity index (VI) — Because air compressors often are subject to extreme operating temperatures, a high VI is essential. The higher a lubricant’s VI, the more stable its viscosity is over a wide range of temperatures.
Adequate pour point and flash point — These ensure that the lubricant will maintain proper flow and operate safely across the application’s full temperature spectrum.
High thermal and oxidative stability — These properties help support a long service life for the lubricant. Without them, rapid oxidation typically occurs, shortening oil life. Oxidation also promotes the formation of sludge and varnish that impede compressor operations, leading to more frequent maintenance with increased costs and downtime. All oils eventually degrade due to oxidation over time. The slower this process, the better — particularly in the demanding operational environment of modern air compressors.
Low oil carryover — In most industrial applications, a small amount of oil carrying over into the compressed air supply is not problematic. Excessive oil carryover should be avoided, as it leads to greater lubricant consumption and the need for more frequent top-offs — wasting oil and money. Lubricant properties which help minimize oil carryover include:
- Low volatility and vapor pressure
- Low foaming
Excellent wear protection — Good anti-wear properties are vital to keep moving compressor parts (such as bearings, gears, cylinders, rotors or sliding vanes) moving efficiently and in proper condition. This is especially important for compressors facing extreme loads, shocks or pressures. Minimizing wear helps keep components running longer, reducing the risk of breakdowns and decreasing the frequency of downtime for costly maintenance and repairs.
Efficient water separation — Many air compressor applications, particularly those in humid environments, are prone to producing significant amounts of water via condensation. Good demulsibility (water separability) matters because if the water and oil don’t separate well, the water can:
- Reduce the lubricant’s viscosity and load-carrying capabilities
- Increase oxidation, foaming and air entrainment, shortening the lubricant’s service life
- Promote rust and corrosion of compressor parts, resulting in greater maintenance costs and downtime
Good demulsibility makes water removal easier, reducing the risk of water-related problems.
Rust and corrosion protection — Corrosion and rust damage components and may lead to failure. They also contaminate the lubricant and may promote faster oxidation, increased wear, sludge formation, filter blockage and other problems. Rust and corrosion inhibitors help protect the lubricant and the compressor components from these issues.
Resistance to foaming and air entrainment — Foaming (a persistent layer of bubbles on the surface of a lubricant) may promote oil carryover and excessive lubricant consumption. Air entrainment (small air bubbles finely dispersed throughout a lubricant) is normal for many compressor applications and is usually not a problem.
Seek Expert Guidance
The best and easiest way to identify the right lubrication solution for your customers’ specific needs is to consult knowledgeable experts such as Isel. With more than 20 years of experience researching and developing specialty lubricants, Isel offers one of the widest ranges of air compressor lubricants on the market. All Isel air compressor lubricants offer outstanding protection and exceptional fluid life. What’s more, they are top-off compatible with equivalent OEM and aftermarket formulations, so no flushing is required. Contact us for more information and help selecting the appropriate Isel lubricant for your customers.
Relevant Entries in this Category that May Interest You:
Isel is Now Part of DuBois Chemicals!
In 2020, Isel joined the DuBois Chemicals team! DuBois/Isel is proud to continue the tradition of manufacturing refrigeration solutions specializing in...
Read MoreISEL to exhibit at Best Practices Compressed Air EXPO – 2021
Visit ISEL at the Best Practices Compressed Air EXPO which is held at the Renaissance Schaumburg Convention Center Hotel in...
Read MoreMAKE-A-WISH TURNS 40 AND ISEL SHOWS THEIR SUPPORT
April 2020 On April 29, 1980, the first wish was granted. A seven-year-old boy who yearned to be a police...
Read More